The Hanford Field Office and tank operations contractor Washington River Protection Solutions are working with a local business to create a full-scale mock-up for the next phase of liquid radioactive waste pretreatment.
Office of Environmental Management
February 4, 2025Craft workers with Hanford Field Office contractor Washington River Protection Solutions view the proposed waste pretreatment process unit full-scale mock-up.
RICHLAND, Wash. — The Hanford Field Office and tank operations contractor Washington River Protection Solutions (WRPS) are working with a local business to create a full-scale mock-up for the next phase of liquid radioactive waste pretreatment.
Over the last three years, the Tank-Side Cesium Removal (TSCR) System demonstration project has treated more than 830,000 gallons of Hanford’s underground tank waste to prepare for feeding it to the Waste Treatment and Immobilization Plant for vitrification, or immobilization in glass.
Lessons learned in building and operating TSCR are helping to design process units that will remove radioactive cesium and solids from waste in Hanford’s 200 East and West areas prior to treatment.
“We continue to make great progress toward starting to vitrify waste from Hanford’s large underground tanks,” said Janet Diediker, federal project director for Tank Waste Operations. “But we’ve known that TSCR was a near-term solution. We had planned for a higher-capacity pretreatment system to feed the vitrification facility.”
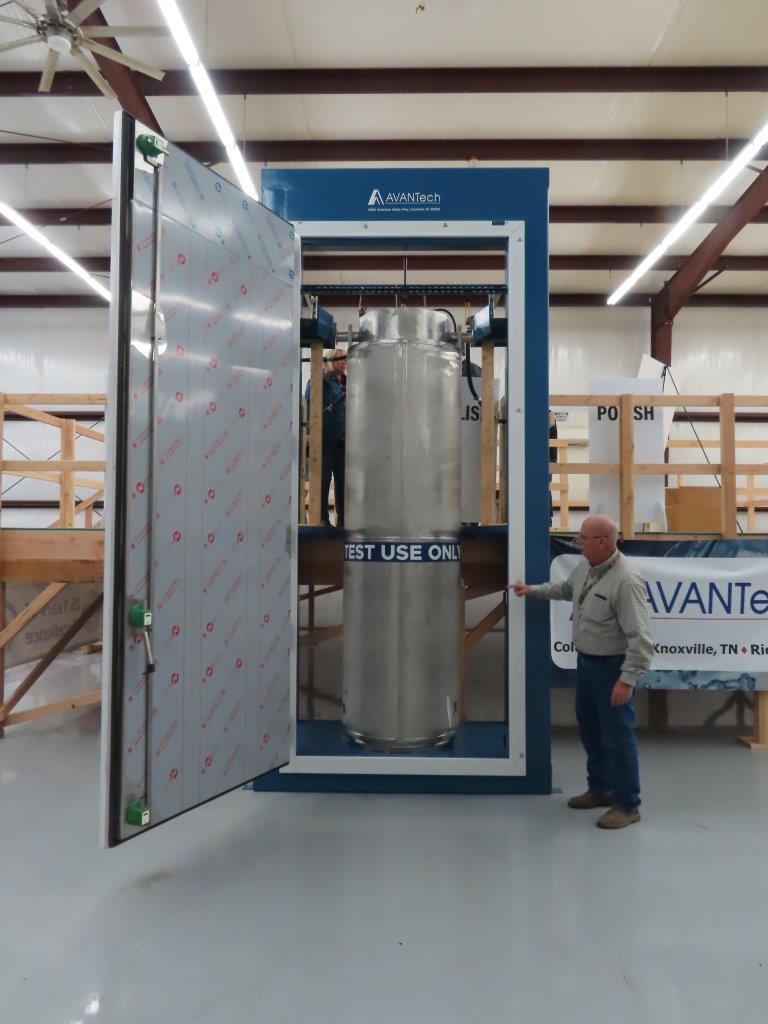
Project Manager Randy Havenor with Hanford Field Office contractor Washington River Protection Solutions demonstrates how new ion exchange column access doors will be wider and taller to make it easier to install and remove the columns.

Blue tape on the mock-up floor marks where the wall of the Tank-Side Cesium Removal System process enclosure ends, illustrating the larger size of the new waste processing units.
One of the first steps in designing these units is constructing a mock-up so workers can get a sense of the improvements. The company designing, fabricating and testing the process units, AVANTech, has built a mock-up of one of the units in its Richland, Washington, warehouse. Workers recently toured the facility to gain valuable insight into how the new layout, piping and hose configurations will improve efficiency and ergonomics.
“We had more than 200 lessons learned documented from TSCR,” said Laura Cree, WRPS project engineer, “and one was that it was a tight fit when trying to change out an ion exchange column, which removes the cesium from the waste. The new process unit configuration put a lot of the piping under the grating, and the floor is higher, so pipefitters have an easier time reaching the piping to disconnect or connect the columns.”
Pipefitter Ivan Howard, who has been working on TSCR since it started processing waste in January 2022, likes the improved design.
“The piping connections on this mock-up are a lot lower; they’re now about mid-chest level,” said Howard. “When you’re in there for hours disconnecting or connecting an ion exchange column, it can get difficult to keep your arms over your head. So having the connections at chest level is much more comfortable.”
The units will also be larger, measuring more than twice the width of the TSCR unit, and longer to accommodate an additional ion exchange column, increasing the system from three to four columns.
Throughout process unit design, workers will continue to use the mock-up to provide worksite analysis, feedback and improvement ideas to help the next generation of waste processing units be more efficient and worker friendly.
To see more on the mock-up, watch this video.